Technology
More than 2000 installations in 5 continents guarantee our brand.
TANGENTIAL CERAMIC ULTRAFILTRATION
In tangential ceramic ultrafiltration, a physical barrier is used, and a pressure pump that make solids in suspension, viruses, bacteria, and other substances circulate in a tangential way though a porous superficies that is in charge of the physical separation, to produce highly pure water.This technology is applied in the separation of raw materials and sub products, in the recovery of chemical agents used during industrial processes and the depuration to comply with the discharge standards.
Nowadays, it´s successfully used in the cosmetic industry, in the potabilization of water and in drug recovery; furthermore it has a great projection in the water depuration of other industries, like food and dye industries.
C&G IBERICA has also developed very specific projects in the galvanic industry, for the maintenance of cataphoretic lacquer.
Technical Description
The tangential ceramic ultrafiltration (UFTC) process is applied in processes where a highly charged industrial effluent is found.In these cases, where traditional biological reactors need considerable time to degrade matter, it´s preferable to previously separate waste, in order to facilitate a quick high quality biological degradation afterwards.
The UFTC equipment is integrated by two accumulation deposits, one pressure bombing system and the ceramic filters.
There´s also a secondary hydraulic system that is responsible of cleaning membranes countercurrent to maintain the performance of the system.
- RETEINED: Is where the water intake is carried out by means of a level probe and they are supplied as the closed circuit is emptied due to the leakage of filtered water.
- PUMP: Carries out the recirculation of the water at the tangential speed required by the membranes manufacturer.
- UFTC FILTER: The two separative flows are carried out, on the one hand the filtrate and on the other the retained.
- FILTRATE: Deposit where filtered water is storage to use afterwards in countercurrent washing or for chemical cleaning when required.
The main advantages of the UFTC system is that allows the separation of pollutants in highly charged industrial water, retaining considerable fractions, but being able to maintain the subsequent biological activity by means of a traditional system of depuration by active sludge, biological or by a bioreactor with membranes (MBR).
Ceramic membranes have a high chemical resistance, mechanical and thermal stability, and a high duration. They can carry out backwash with air or with highly corrosive chemical products, which means we will always have an optimum capacity of filtration, and as a result a high quality effluent.
TUBULAR ULTRAFILTRATION
The tubular ultrafiltration process is mainly use for two activities: First, we can find depurators that don’t have a biological reactor, but they have a secondary treatment system. Second, it can be apply in superficial waters like lakes, rivers or wells.For waters with urban or industrial origin, tubular ultrafiltration allows us to have an effluent with the right quality to reuse. For superficial waters, the tubular ultrafiltration process, allows us to turn treated water into drinking water.
The tubular ultrafiltration equipment is arranged in series with the other elements of the installation, in a way that clarified water goes through one side and solid waste goes through the other.
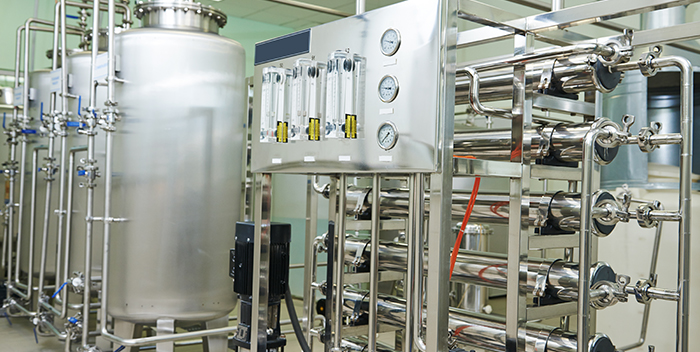
REVERSE OSMOSIS
Introduction
The reverse osmosis process separates water from its contaminants by using semipermeable membranes. These contaminants can be: dissolute solids, organic or inorganic products, viruses, bacteria, etc.
The process is known as “reverse” osmosis, because an external high pressure is needed to make water go through a membrane leaving behind all impurities. Reverse osmosis is capable of separating up to 95%-99% of total dissolute solids (TDS) and 99% of all bacteria, producing low mineral pure water.
Almost any type of water can be treated with reverse osmosis. To get the most out of this technology, water has to be treated before going through the membranes of the reserve osmosis. This tends to be necessary in a lot of cases as the membranes are fragile and tend to become clogged.
To avoid having to frequently clean or substitute the membranes, some pre-treatments are made, like: water softeners (removal of hardness), active carbon filtration (elimination of organic substances), ultra-filtration (elimination of oil and grease), evaporation (salt removal), etc.
General description of operation
The osmosis pump (P1) sucks the solution that must be driven at 18,20bar, in order to go through the reverse osmosis membranes (M1, M2).With theses membranes a filtration of the ions is made, resulting in high quality water that can be reuse.
The permeate, osmotized water, is store in an accumulation tank (T2), located in the same structure of the equipment, from there is send to its place of application through a centrifugal pump (P2).
The system has installed:
• Two manometers, to visualize any obstruction in the membranes.
• A high pressure switch that would stop the machine with an alarm.
• Two flow meters that allow seeing the flow in l/h of concentrate (rejection) and of permeate (osmotized water) produce in the process.
PRINCIPAL COMPONENTS AND ITS FUNCTION
Osmosis pump “P1”: It sucks the water of the recollection tank “T1” and sends it to the osmosis membranes. With this high pressure pump, we can reach the necessary flow and pressure to have a high quality permeate as a result. This pump is equipped a level control “LC1” that prevents dry operations.Washing and re-send permeate pump “P2”: It sucks the osmotized water accumulated in tank “T2” and sends it to a reserve tank for its reuse. Level control “LC2” avoids dry operations.
This pump is also use in all the operations that involve maintenance and cleaning of the membranes.
Pre-Filter “F1”: It is installed before the osmosis pump to avoid noxious particles from harming the pump.
Osmosis Membranes “M1” and “M2”: Using reverse osmosis they do the de-ionization of the water. To control the state of any obstruction there are two manometers installed, “P11” and “P12”. While for its security a pressure switch “PC” is installed at 20 bar.
Applications
To this day, reverse osmosis technology has numberless applications, some of them are: water potabilization, rationalization of the productive cycles, energy saving, decontamination, water recovery and important substances for the productive process.Industrial sectors where this technology is apply:
• Drinking water production.
• Water production for vacuum generators.
• Ultra- pure water production for the electronic industry and semiconductors.
• Cosmetic and pharmaceutical industry (antibiotics, insulin, amino acids, etc.).
• Food industry (fruit juices, animal blood, etc.).
• Galvanic waste treatment and recuperation of metallic salts.
• Hospitals and labs.
MEMBRANE BIOREACTOR (MBR)
Membrane bioreactor (MBR) technology is based on the combination of a biological biomass suspended reactor, responsible for the degradation of the organic compounds, and a separation by filtration of porous membranes, responsible for carrying out the physical separation by difference of pressure between the two sides of the membrane.This technology has a series of advantages in terms of protection of water resources, thanks to the high quality of the treated water.
The quality of the water, in particular the absence of suspended solids and turbidity allows MBR to be considered as the perfect tool for pre- treatment, before desalinization or the preparation of high quality water.
On the other side, given its modular condition, MBR can be great for the development of wastewater network in urban areas.
Among the principals uses of MBR are: the enhancement of the capacity and water quality in conventional plants, and the total or partial reuse of the depurated water. It is ideal in plants that have small surface.
This technology can be applied in different sectors. Great results have been obtained in diverse in industries as diverse as the food industry and the cosmetic industry.
Technical Description
Depuration through MBR (Membrane Bioreactor) is an active slugged process, in which depurated water is not extracted by sedimentation in a secondary decanter, but by filtration through membranes. In conclusion, it is a mixture between a biological reactor and the subsequent ultrafiltration.Considering it situation there are two types of membranes for MBR:
- External membranes or with recirculation to the bioreactor
- This configuration of MBR implies that the water is recirculated by means of an electric pump, from the bioreactor to the membrane unit that is externally disposed.
- One part of the water is filtered while the other is forwarded to the reactor in order to degrade more organic particles. These types of membranes are tubular and need to be contercurrently clean with an automatic system.
Submerged membrane
The membrane unit that performs the physical separation in immersed in the biological tank. The driving force through the membrane is achieved by pressurizing the bioreactor or creating negative pressure in the permeate side. The membrane is cleaned by frequent backwashing with permeate water and air, occasionally by backwashing with chemical solutions.Taking into account a series of important advantages and the excellent quality of the treated water that is obtained, the MBR´s economic balance is positive.
MBR technology is especially competitive when some of the following conditions appear:
• The need to decrease the production of biological sludge (up to 80%).
• The need for a high degree of purification: discharged into public waterways, sensitive areas or payment of a high discharge rate.
• Reuse: may be imposed by the scarcity of water in the area or it can represent an important added value to be considered. The variables here are going to be: the price of the cubic meter of water or the subsidies for reuse.
• Small available space.
• The increase in the capacity of conventional existing treatment plants.
• Industrial effluents with difficult or slow biodegradability components. MBR technology allows organic matter considered to be poorly biodegradable for other types of more conventional technologies.